Sunday, December 25, 2011
3D-Printed Mouse
http://web.media.mit.edu/~mellis/mouse/
Pretty cool. The idea is to be able to print some kind of mouse "add-on" for my device too as well and thought someone already must have done it. And I found the above... Anyway, I will see if I use that design, http://www.thingiverse.com/thing:1056, or something else that may show up...
Wednesday, December 14, 2011
Blender 2.61 Released!
* New Render Engine (Cycles Render Engine)
* Motion Tracking
* Dynamic Paint
* Ocean Simulation
Check it out here!
http://www.blender.org/development/release-logs/blender-261/
Thursday, December 8, 2011
Tuesday, December 6, 2011
TreadGaming Black Enclosure
I've used ABS plastic before, and now I decided to try using PLA instead. I basically used the same settings I used for ABS, and just changed a few parameters. It ended up not bad, but still needs some tweaking. Anyway, here are some photos of the 3d print. Note also that the camera really sucks at close ups, and I was seriously thinking investing in a better one...
In the end though, I will probably have a few different enclosures one can choose from, depending on what one want to do with the device. For instance, I was also thinking making a "mouse" add-on plastic part where this will transform into a mouse, fitting nicely into one's hand...
Oh, and also, I will probably add some logo on there somewhere. And maybe experiment with some other designs, as I have almost reached the practical goal, where the enclosure is finished enough to be useful. That includes distance from lens to surface, headers available, and the lid good enough to stay in place... Also, I was thinking adding stripes or something so it will be easy to use strings to tighten the whole thing onto whatever surface one want to use.
Sunday, December 4, 2011
10 TreadGaming PCB's Have Arrived!


Sorry, the camera sucks at close-up.
MyRO PCB was little slower this time around, and late about 1 week. However, I'm not really in a rush. I got it all really nice wrapped up, so a lot of care taken there. Also, I got 2 calendars with both Canadian and Chinese red days marked on it...
Saturday, December 3, 2011
Wednesday, November 23, 2011
Printrbot - A little RepRap 3D printer
It looks quite nice though. My MagerGear RepRap Prusa Mendel is more for hobbyists/advanced users, while this Printrbot will make it easier for most people.
http://printrbot.com/
And it's a Kickstarter project: http://www.kickstarter.com/projects/printrbot/printrbot-your-first-3d-printer
Makes me wonder what will come next in the 3D printer area, as this is under continuous development because it's all open hardware/source and always under development and improvement...
Friday, November 11, 2011
jDome
It would be quite cool to have one in front of a treadmill and my device though! :)
http://shop.jdome.com/en/
Thursday, November 10, 2011
Wednesday, November 2, 2011
My Nature Academy Certificate!
Wednesday, October 26, 2011
Monday, October 24, 2011
The Gadget Show - Ultimate Battlefield 3 Simulator
Sunday, October 23, 2011
Opendous Doing Some More Tests





The hardware really looks promising, and I was planing do a minor batch of around 10, so I have a few more to test with, and can send them out for others to review and test, before I do a major batch!
Wednesday, October 19, 2011
Blender 2.60 Released!
Features:
http://www.blender.org/development/release-logs/blender-260/
More Features:
http://wiki.blender.org/index.php/Dev:Ref/Release_Notes/changelog_260/More_Features
Sunday, October 9, 2011
Opendous Doing Some Tests






I've also tested the UART serial communication using the Micropendous3 board I bought before, and using code Opendous have written for the board. It works! I really appreciate the help here, and there are more tests to come! For instance, EMI testing and test the board in -30C cold to 70C degrees heat...
Tuesday, October 4, 2011
Gamercize
Gamercize Pro-Sport Cycle and Gamercize Pro-Sport Stepper £139.90. Seems you can only pick one platform for it? So, either PS3, XBox360 or Wii... which is kinda bad... would be better if it worked on all platforms... or maybe it does?
One important thing to note here though, is that the device doesn't seem to be sending movement events, but only disable the controller when there is no activity. So, basically that means you can only play the game while using their device, but there is no mapping between the game and device. For a PC it can disable the mouse.
Thursday, September 29, 2011
Make: Live - 3D Modeling & Printing
However, kudos to Bre Pettis for mentioning RepRap's though. But again, not enough focus on RepRaps...
I couldn't find a link to a full video streaming online, so I will update this post when it arrives. In the meantime, you can use this link:
http://blog.makezine.com/archive/2011/09/make-live-92811-3d-modeling-printing-video.html
or even better, get the full video from Miro using this feed:
http://blog.makezine.com/feed
Tuesday, September 27, 2011
100 Avago ADNS-9500!

I ordered them so I would have "only" 100 in stock, for when production starts! Problem is that most only have minimum of 1000, while others have a lead time of 20+ weeks... So I thought I stock up some now while I can. I can even send these to MyRO PCB, so they have them in stock for production...
I found a place where I could get 100, namely RS Online! I figured that when I do create the high quality product, 100 shouldn't be all that impossible to be able to sell in the world...
Sunday, September 25, 2011
EEVblog #203 - Melbourne Hacker Space Visit
Saturday, September 17, 2011
The Golden Age 3D - Official Trailer
Saturday, September 3, 2011
Opendous Assembled My PCB

So, Mr. Opendous, the guy behind Micropendous that helped me out with the PCB, received a PCB board from me to use as he offered to test it. This is the assembled board, and I thought it looked so nice that I thought I post about it. As you can see here there are four standard sized headers and one smaller exposing a bunch of inputs/outputs which can be used to extend this PCB's functionality. It's really easy just to add a button for instance. Also, some have PWM support meaning you can have values between 0-255 for instance, instead of boolean 0 or 1.
Wednesday, August 31, 2011
The Golden Age 3D
All made in Blender using the knowledge from that I suppose... Awesome isn't it?
Monday, August 22, 2011
Collected Blender Resources
Blender 2.59 was recently released, and I can't wait for the 2.60 release which will include Google Summer Of Code stuff as well! You can do stuff like this:
(camera tracking and dynamic paint)
Blender 2.59 has cool add-ons such as:
* Ivy generator
* Sapling (Create trees)
And Blender 2.60 is supposed to be out in a month or so... end of September... And will supposedly also include Cycles!
Fun with Cycles from Jikz on Vimeo.
http://www.blendercookie.com/2011/05/02/feature-preview-cycles-render-engine/
Ton Roosendaal Interview at Siggraph 2011
(original creator of Blender)
Blender Foundation - Siggraph 2011 from 3DTotal.com on Vimeo.
Also, pay attention to the screen in the background showing some awesome renders done in Blender.
News:
http://www.blender.org/
http://www.blendernation.com/
Tutorials:
http://www.blenderguru.com/
http://www.blendercookie.com/
http://www.benamend.com
http://blendernerd.com/
http://www.blendercycles.com/tutorials
http://blenderdiplom.com/
http://www.blendtuts.com/
There is a lot going on with Blender these days, and I can only see it increase! Blender is really taking shape. Which remind me... this is also quite entertaining to watch:
Reasons why I want to punch Autodesk Maya in the face... from Josh Robinson on Vimeo.
And there is a new Node Particle System coming up for Blender:
http://phonybone.planetblender.org/
Sunday, July 31, 2011
The SULSA - 3D Printed Aircraft
More about it here:
http://www.southampton.ac.uk/mediacentre/news/2011/jul/11_75.shtml
Wednesday, July 13, 2011
Friday, July 8, 2011
The RunningMan
Note that I just use 10 frames, so yea, the texture jumps a little.. whatever dude!
Note also, that this is just me playing around in Blender... Pretty cool though, eh? Maybe I will see if I can animate the figure too...
Thursday, July 7, 2011
2 Logo Winners from crowdSPRING

I liked this overall, and the one I got also was more of a complete logo version as for a web site. It conveys hard core gaming. Also, the figure there could be animated for even more enjoyment.
What I liked here was the simple figure there, which also was quite nicely integrated into the text itself in another example I got (notice legs look like the letter "r"). However, I like how that figure is easy, but still kinda cool - looking like running. It will be quite easy to stamp that on the enclosure for example.
So, currently I'm working on trying to combine these two somehow to the ultimate logo... :)
Tuesday, July 5, 2011
Do you think Blender sucks? Well, think again...
Thursday, June 30, 2011
Treadgaming Blender Logo Animation
Thursday, June 23, 2011
Blender 2.58 (stable) Released!
Blender 2.58 update log
The majority of work for 2.58 went into fixes with over 200 bugs fixed since last release but there are also quite a few useful additions worth checking out.
Prominent features (the cool stuff)
Warp Modifier:
This deformation modifier can be used to warp parts of a mesh to a new location in a very flexible way by using 2 objects to select the "from" and "to" regions with options for using a curve falloff, texture and vertex group.
Render Baking:
For high polygon models it is now possible to bake multi-resolution models using much less memory than before. There are also new bake modes: specular color, specular intensity, mirror color, mirror intensity, alpha (transparency), emission (glow)
Empty Images Display:
Instead of using background images or creating meshes with materials and image texture it's now possible to assign images directly to empty objects to use as reference images. They display in all draw modes and can use object draw options like XRay to draw over other objects.
Sculpting:
Constructive modifiers (like subdivision surface, mirror and other) were supported for sculpting mode. Sculpting could be not very accurate with such modifiers enabled, so there is a new option in the toolbar to disable applying constructive modifiers in the sculpting session.
Mesh Inset (Addon):
Mesh inset is a very useful tool with the ability to inset individual faces or a selected region.
Camera Locking:
It is now possible to move the camera using normal view port navigation by enabling "Lock Camera" in the "View" panel.
And much more! Please check the link.
Wednesday, June 22, 2011
Treadgaming Logo at crowdSPRING
http://www.crowdspring.com/project/2299107_treadgaming-logo/
The award is the lowest because I'm testing it out, and I thought it would be interesting to see what I can get for that price...
Tuesday, June 21, 2011
Designing the Enclosure
So, I'm not by any means done. Details will be added in time. But for now, I want the right sizes to be in place. Then, I can create some nice round corners and basically smoothen it more. I was also planing creating a plastic-only solution, with some kind of snap-on, snapping on the top part because that way I will avoid extra material, such as screws...
Animation created using Blender and GIMP. Note that this is only the bottom part...
Monday, June 6, 2011
The Ben Heck Show - Building a Custom 3D Printer
Saturday, June 4, 2011
Guess The Print
Friday, June 3, 2011
Almost Perfect 3D Print
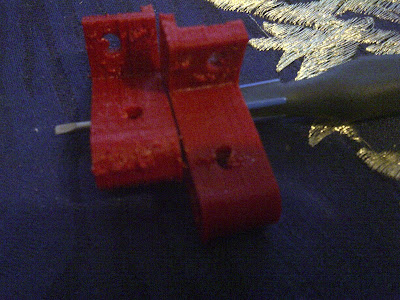
You are most likely having an extruder not retracting properly. If it's going too fast you should also be able to hear some buzzing sound coming from it.
The helpful and friendly djw_ohio in the #makergearv2 channel helped me with this so a big thanks to him. Thanks to him, I now can print like so:
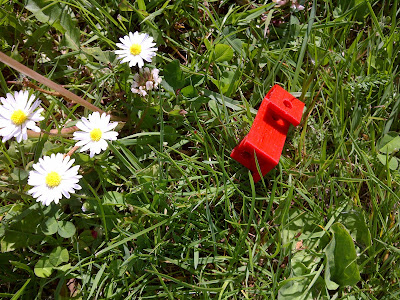
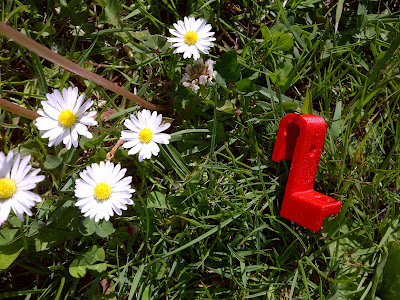
Isn't that just beautiful!
What I did was the following:
Change the "Extruder Retraction Speed (mm/s)" in the "Dimension" tab to 18.0, but noticed that it didn't extrude anything when it was supposed to print smaller areas, so I decreased this to 15.0.
You can also test this in Repsnapper by remembering that in Repsnapper it's mm/min, but in Skeinforge it's mm/sec. That means, take the value in skeinforge and multiply that by 60, and use that as "speed" in the Print tab (under "Interactive Control" tab). When I did this I noticed that the value 25 in skeinforge (25 * 60 = 1500) was waay to much for it using the Sprinter firmware I've now changed to.
I also set the "Restart Extra Distance (millimeters)" from 0 to 0.015. Not that I may have to, but 0 may not be totally right. Particularly because I had some issues with the filament not being extruded in time. This value is one of those that probably needs to be tested some more though.
Next I changed the "Layer Thickness (mm)" from 0.4 to 0.3 and "Perimeter Width over Thickness (ratio)" under "Carve" from 1.4 to 1.1666667. Why? Well, that means 0.3 layer thickness times 1.1666667 = 0.35 extrustion width which is is the size of my nozzle. Actually, my nozzle extrudes ~0.43mm, but this will do for now... Will update on this when I know more...
Furter, djw_ohio explains:
"If your nozzle was 0.35, and your layer height was 0.35, you would print a perfectly round thread. At 0.35 nozzle, and 0.4 height, it got 0.05 slop in where the extruded filament lands. With a layer height of 0.3 it doesn't have any room to wiggle around before it hits the print bed. You can get any width you want really. You can use a 0.35mm nozzle and print 0.7 if you feel like it. If you slow down the feed rate, and keep squeezing just as much filament out, it makes the lines fatter."
This is quite important as per default, skeinforge is set for a 0.4 nozzle, but mine is a better 0.35 one.
"Infill Perimeter Overlap (ratio)" under "Fill" is now also set to 0.26.
"Thread Sequence Choice" was changed from "Loops -> Perimeter - > Loops" to "Infill -> Loops -> Perimeter" because that way the perimeter can get wrapped around the infill, even in mid air.
Tuesday, May 31, 2011
EEVblog #175 - Project Sagan
Monday, May 30, 2011
3D Printing Meetup
More about it here: http://www.publicknowledge.org/blog/3ddc-video
Fast access to videos:
Thursday, May 26, 2011
More Advanced 3D Print Succeeded (And Steps Per Unit)
float x_steps_per_unit = 160; // (360 / 0.9) * 16 * (5 * 8)
Values explained:
- 360 - This is how many degrees there is in a circle to make a loop (full rotation).
- 0.9 - This is the motor's Step Angle.
- 16 - Microsteps (1/16).
- 5 - Length/Pitch between cogs (mm).
- 8 - Amount of cogs in the pulley.
float y_steps_per_unit = 160; // Same as x.
float z_steps_per_unit = 2560; // ((360 / 1.8) * 16 ) / 1.25
Values explained:
- 360 - This is how many degrees there is in a circle to make a loop (full rotation).
- 1.8 - This is the motor's Step Angle.
- 16 - Microsteps (1/16).
- 1.25 - The thread pitch of the z-threaded rod.
For e, the extruder, I had 1479.31034482758620689655, which was basically calculated like this:
- Mark up 100mm on the filament from the extruder.
- Set a suitable speed in repsnapper, so the filament doesn't slip.
- Set 100mm in length to extrude.
- Press "Extrude" and let it do it's work.
- Calculate new value by using the value set and divide with, as exact as possible, how much filament actually was pulled in and multiply that with 100.
However, after a recent chat in the support channel this is what I use instead:
(360 / 1.8) * 16 * (13.6 / 31) = 1403.9
float e_steps_per_unit = 1403.9;
Values explained:
- 360 - This is how many degrees there is in a circle to make a loop (full rotation).
- 1.8 - This is the motor's Step Angle.
- 13.6 - Gear Ratio (13.6:1)
- 31 - Circumference in mm.
This value is probably pretty much spot on. The following is printed using these values:


It's not totally perfect, as you can find a few filament loops here and there. They are there mostly because it can't print in the air... Still, this can probably be tweaked some more... but, not bad. Not bad at all.
There have been issues with the filament not sticking and clogging up to the nozzle, ruin the print when the nozzle came back for round two - the next Z layer. I tried to heat the bed higher than 100C, but it doesn't seem to go much higher than that. Or, it will take crazy longer time. Either way, I used Acetone on the board and I believe this actually is the main reason the filament stuck straight away for this print. Well, basically there are 3 parameters that needs to be great.
- Height from the nozzle to the heatbed.
This is around 2mm...
- Temperature of the filament. I used 220C this time. Didn't seem to "drop" out as much when the extruder was idling.
- Heatbed hot enough (May not be needed for PLA plastic). I had close to 100C. 95C+. Seems hot enough. At least for this ABS print. It didn't want to stick before even if the heatbed was around this temperature, but I'm guessing this is because of all the in-purities from fingers and such.
Again, I'm guessing the Acetone helped a lot by cleaning away all finger fat on the bed, and this time around I also heated the bed way before the extruder. The bed takes longer to reach the higher temperatures anyway, but it's probably a good idea to heat that up well enough before starting the extruder.
I will probably do a post later on with files and parameters collected, for newcomers to start easier. I wanted this information about the "steps per unit" out already though as it's quite impossible to find using your favorite search engine...
Tuesday, May 17, 2011
First Acceptable 3D Print!

After A LOT of tweaking and testing, this is what I ended up with. Naturally, I'm not done yet, but I seem to have the basics down now!
This camera I used is better too apparently...
What you see there is a test rectangle made in OpenSCAD using this:
difference() {
cube([100,100,10], center = true);
cube([99, 99, 20], center = true);
}
.. and this is printed with 230C extruder, and heatbed at 80C. Red ABS plastic. The scaling for X and Y isn't proper yet, so that is next on the ToDo list... Z seems pretty correct. Measured 10.04mm on this one. X and Y here is 38mm... should have been around 100mm...
A BIG thanks goes to Rick, OhmEye, tommyc, Kliment, ScribbleJ, prusajr and everybody else in #makergearv2 and #reprap channel at FreeNode! Been hugely helpful and patient! I'm not done yet, but this sure is a great milestone!
Sunday, May 15, 2011
3D Printing Software Is Currently A Mess
I also had some odd issue where the platform wasn't moving in X when printing... It moved in Z and Y, and I could move the platform quite easily both by hand and using the "Interactive" tab in repsnapper.. but after heating up extruder and the bed, and pressing "Print", it got stuck and wouldn't move in X, even though it seemed the motor tried to move the platform. Maybe it had too little power (amps) when everything was on.. could be wrong firmware, or the generated gcode was bad... not sure. Since I did it all in repsnapper (even generating the gcode), I'm quite sure the main problem was that this version of repsnapper couldn't print!
There were a lot of filament waste too, as I really though it was a problem when the filament curled up and got stuck on the side of the nozzle. I though it was supposed to come straight down. Particularly ABS plastic. But, apparently this is rather normal, and really, the distance to the surface will be so short, that it won't be able to curl up like it did. So, time wasted unmounting the extruder a few times, and seeing that it looked fine. No leakage in the heated barrel either. Also, you need to tweak the spring mechanism that holds the filament in the extruder. Too loose, and there isn't enough force to hold it. Too tight, and the filament will slip... or, well this is more a problem if the extruder moves too fast...
There are many different firmwares and different versions of the software used to print and slice (break down an object into layers). I liked "repsnapper" as it was more intuitive, but.. well, if you go to: http://reprap.org/wiki/RepSnapper_Manual:Introduction and use https://github.com/timschmidt/repsnapper which is supposed to be the one you should use (as it's the one currently being updated), you are surprised by print not working. Even when trying to build the other (http://svn.kulitorum.com/RepSnapper), you get a message to use the https://github.com/timschmidt/repsnapper one). I checked out the "master" and then went back a few months (git hash: 83d3017625f5e65116da80f8fcc7df7f36737b3f), to get a working version. However, I noticed that that version isn't totally correct either as under the "Print" tab there was supposed to be a slider for changing the speed of the extruder. And, in that version I had checked out, no slider can be found. Confusing. Especially for me as a Linux (Ubuntu) user. Windows users have a prebuild one already...
So, for repsnapper, I now use http://svn.kulitorum.com/RepSnapper, ignoring the message of it being deprecated. And, voilà ! Now I seem to use what everybody else are assuming you are using... If you use the Windows version, you are using this version too. So, to sum that up:
USE: http://svn.kulitorum.com/RepSnapper until https://github.com/timschmidt/repsnapper is better!
And then we have skeinforge... The UI isn't particularly beautiful, and it's rather confusing and not as intuitive as repsnapper. However, one can see it being useful, as there are many more options there, so you really have control over many things. Besides, it's supposedly generates better gcode than repsnapper as well. And, skeinforge is only for generating gcode, and nothing else, which is good, as it concentrates on being good at that.
I was using version 039, and apparently that doesn't generate "E" for extrusion per default (for the G1 command). So, it would basically just move the extruder around, not really extrude anything. Now, I've updated to 040 (or 041, not sure which one to use as with 041 the pane was empty under the "Profile" tab...).
Thankfully, the community is really helpful, and everybody agrees all this being bad and I'm guessing all this will be better over time. But as for now, one have to see the software being in alpha stage, although skeinforge feels quite matured (once you get used to it).
Anyway, I'm currently using this to testprint with:

I use skeinforge to generate the gcode. Then I use http://svn.kulitorum.com/RepSnapper to print with by just loading the generated gcode in there. I can also see what's going in real-time with the temperature, and, there is a handy log and "Interactive" buttons. Funny enough, it's not showing the bed's temperature, only the extruder's. The other repsnapper I used (the one with hash mentioned) had both extruder and bed temperature showing). It's really starting to take shape now though. Motors seem to behave as they should.
So, currently, I'm tweaking settings in skeinforge, trying to end up having a nice print following this handy guide: http://www.mendel-parts.com/new_forum/phpBB3/viewtopic.php?f=37&t=256...
Don't get me wrong, I appreciate all the work people have put into repsnapper and skeinforge! I just wished it was easier to get started. I will probably do a post later with everything summed up nicely so newcomers to the 3D printing community have an easier start.
Friday, May 13, 2011
Google I/O 2011
This is also interesting (position is set in the video, so you don't start at the beginning):
Wednesday, May 4, 2011
High Resolution 3D Printing
Possible my next step, hehe... Seems it won't really be available until late this year... or something.. worth keeping an eye on though! Seems the guy wants it for the 3D printing community... not sure if that means everything will be open though...
Sunday, May 1, 2011
Prusa Mendel Almost Assembled

Man, this is fun! Sure, it takes time, but you are also building a cool machine from scratch! I take it easy, and think through every step as much as I can in my head, before actually doing it. You can come up with a few tweaks here and there, and really, you don't have to do exactly what documentation says. I mean, as long as you know what you are doing, you can do things differently.
These differences may even be for the better... For now though, I will just build this to make it work printing. Then I will probably optimize some. Like rerouting wires in the base and just basically clean it up so it looks nice too. And maybe also add a fan and end-stops for Max values (currently you use for Min values, which means motors will stop at basically point 0,0,0 (Home position). You may also want this "Max value" so you for instance can let the Z motor go all the way to the top when a print is done for example). I just love the flexibility you have with this open source/hardware 3D printer!
There have been a few bumps, and redoing during this time, but it's really stimulating to have eureka moments every now and then when you reach certain milestones. I had one when the motors worked, and the first time you move the platform back and forth, you do it for like 10 minutes because it's exhilarating that it works. And just now I used repsnapper to turn the heat on in the nozzle (extruder, hot-end), and checking the temperature. And I was happy to see it worked! It's important to test these things, especially the nozzle because if it gets too hot, that ain't good. I was afraid the thermistor (the component that reads temperature) wasn't properly installed with the crimps. But thankfully it works as it should! Would have been a lot of extra work to expose that part again, as it's in there, in that black thing you see in the picture...
There is a function in repsnapper to set the heat to a certain value, and I was amazed how well it worked. I read the thermistor value periodically, and could see the temperature increase to the set value (in this case 100 degrees Celsius). Then, it went little over (to 110C), and then went down to the set value (100C) and stayed around there. Turning the heat off, and I could also see the temperature drop... I also tested just unplugging the USB to the Arduino, and was glad to see that it means power off to the nozzle as well. That is good news as that means the heat won't continue to increase if you just unplugged.
I was also glad to see end-stops are working. These are important so the motors will stop and also, so it can "go home" and the printer knows where it is, and can use that as a reference for printing.
You communicate over serial with the Arduino 2560, and here are some useful starter commands for reference:
M998 - Turn on pull-up resistors. (Needed for M999)
M999 - Get X and Y endstop values. (1 means not triggered, 0 means triggered)
M105 - Read thermistor temperatures
And here is a list of many more: http://reprap.org/wiki/GCodes
More images and updates to come.... I basically only have to connect the heatbed (the big red thing you see in the picture), and then I'm off to actually try to print something...
Thursday, April 21, 2011
MakerGear's Prusa Mendel Arrived!
Look at the adventure the package had today:



They even included some filaments for me to play with...
So, yea, I will assemble the thing now...
Thursday, April 14, 2011
GameRunner released!
$500 for it, which isn't all that bad. Only problem here is that it will probably weight a lot, which adds to shipping. Currently 4 months wait time... Anyway, I wish them all the best with it!
Again, I'm doing my thing for the experience, and the fun of it. Mine will also be cheaper for those that already have a treadmill.. and, my device works on other things as well. Such as stationary bikes. There are also extra pins (breakout pins from the AVR) which one can use to expand it's functionality. Such as simple buttons. Then it's just up to the software to do the rest (send the appropriate command over USB). I have a few "add-ons" in mind already. But really, adding a few extra buttons is quite easy, and super cheap (a few bucks at most). You really only need wire and the button itself... Besides, there is a lot of flexibility as how people can hook up and place the buttons!
Monday, April 11, 2011
Header Image Updated
Thursday, April 7, 2011
Eureka! It's Alive!
I include an image with the device on its side, also showing the plastic part underneath that is required. Besides, reading blogs with only text can get boring, so having more images makes it more fun. I like that myself.

Tuesday, April 5, 2011
Treadgaming PCB v1.0 is here!
So far I've tested code to simulate a USB gamepad, and I also tested the LED's on it, and it all works! Next is to solder the sensor on and do the real test. But, so far I'm happy with the result!
Just look at that beautiful thing: